Hino Motors began full-scale operation of Koga Plant in September 2017. In this article we take a look at its role as a factory featuring cutting-edge technology and it position as a “mother plant.” We sat down with Koga Plant Manager Masahiro Aso, who spoke passionately about the present and future of the plant while touching on its technology, initiatives, and unique characteristics.
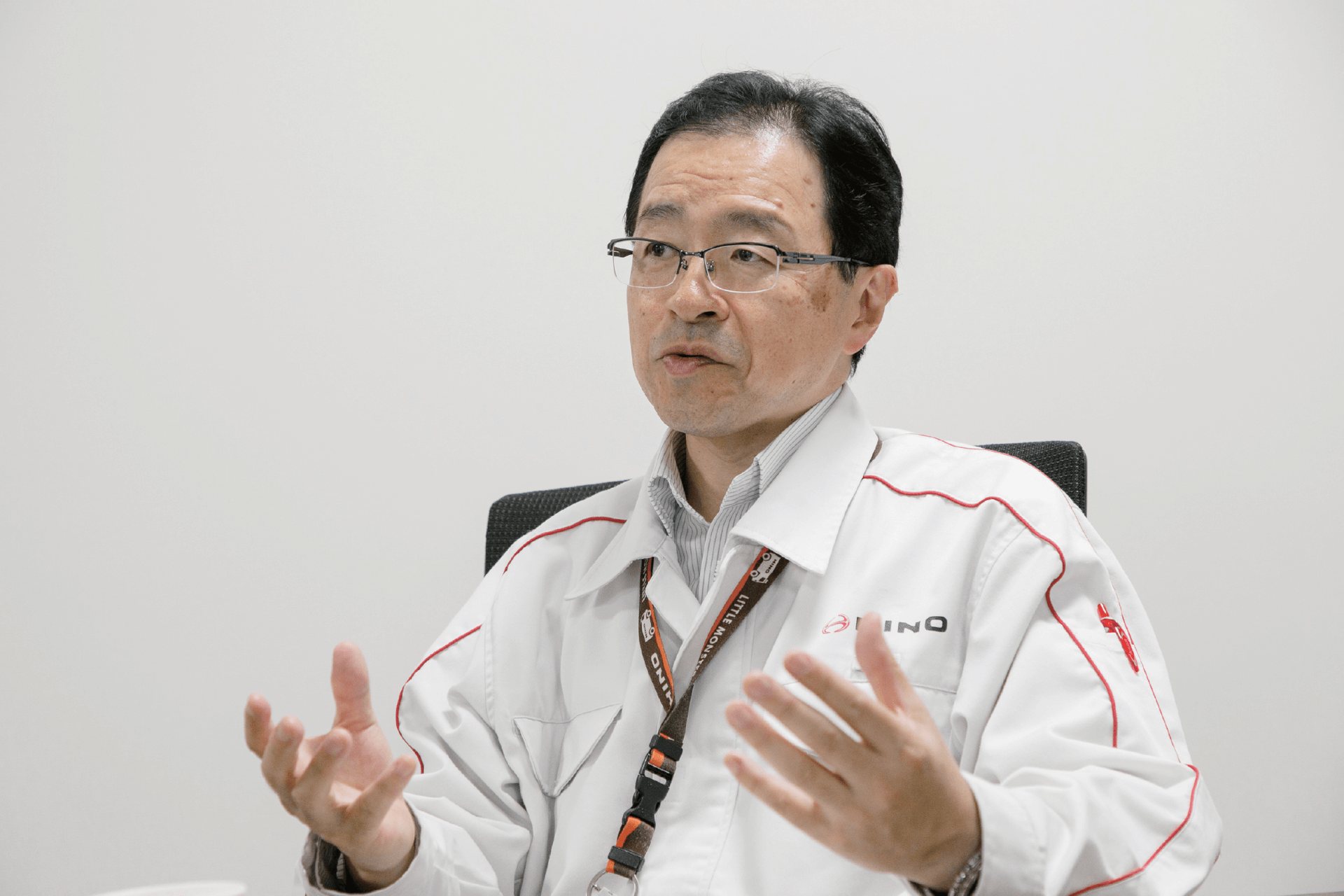
Q: What is the role of the mother plant?
Mr. Aso: First, let me start by telling you about the trucks that we make. Our medium and heavy-duty trucks are commercial vehicles characterized by high-mix, low-volume production. In addition, with the ongoing trend of globalization, overseas sales are increasing yearly and have exceeded domestic sales since 2007. Against this backdrop, our mission as the mother plant is to provide technical support to plants abroad and continuing to disseminate information to support production.
Q: Can you please give us a little more detail about the technology at the Koga Plant?
Mr. Aso: Hino Motors adopted a modular approach to production as one element of our efforts to make best-fit commercial vehicles. Historically, we developed vehicles on a model-by-model basis. We are now making them on a modular basis. Making modular units and using them to assemble the desired vehicle allows us to minimize lead time. The defining characteristic of the technology at the Koga Plant is that it is designed to achieve modular production and realize the benefits I mentioned.
Q: What can you tell us about the use of robotics and automation?
Mr. Aso: We are actively deploying robots at the Koga Plant. We use robots to handle heavy components and do tasks that are difficult for the employees. This serves to both enhance safety and also contribute to consistency when it comes to product quality. In addition, apart from robotics we have also adopted automatic guided vehicles (AGVs) in many processes at the plant to heighten efficiency.
Q: Apart from that, can you tell us about any other areas in which the Koga Plant is superior?
Mr. Aso: Truck frames are normally made by stamping and in batch production, but by introducing a roll-forming machine of our own design, we are able to produce vehicles in a way that is in accordance with the order of assembly. This has allowed us to reduce lead time for customers. Apart from this we use thick metal plate welding methods, which contribute to fewer instances of distortion compared to conventional methods and enables us to both shorten the production process as well as heighten product quality. At Hino, I think we excel at developing and using these kinds of technology.
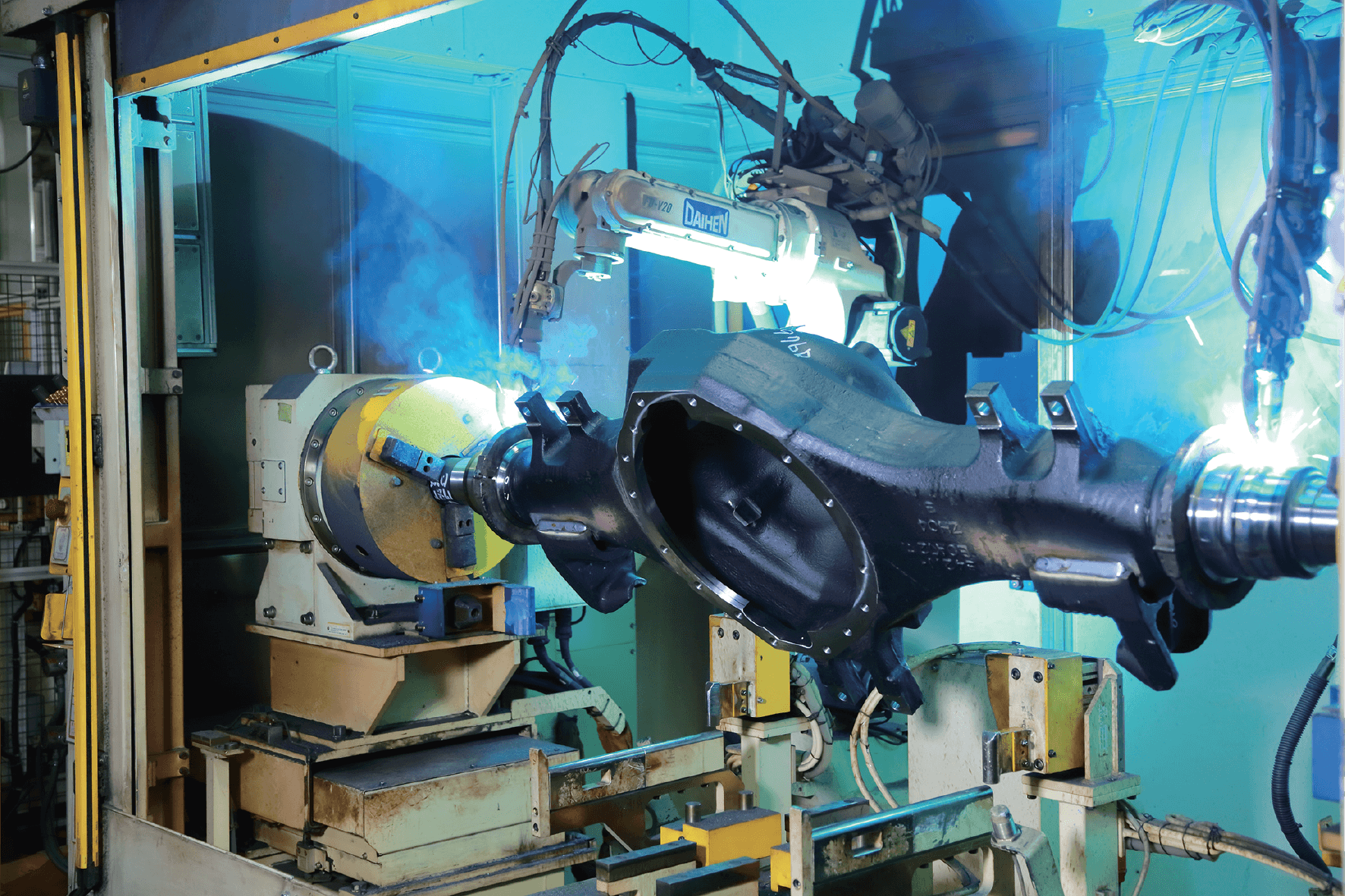
Mr. Aso: In the past, there were some parts that couldn’t be made outside Japan for technical reasons. However, as the technology advances and spreads globally, it became possible for us to produce more of these parts outside Japan, which enables us to combine the components and parts made abroad with those made inside Japan. This has accelerated our production speed outside of Japan. At the same time, automation levels vary by country and region. As such, we still need to teach how to craft things manually. We cooperate by offering technology support on a country-by-country basis.
Q: So, the role of manual craftsmanship is also important in production?
Mr. Aso: Regardless of advancements and deployment of automation and robotic technology, it is important for us to choose what robots should do and teach human techniques to them. I believe that I need to convey the human side of technology. Our people find and make enhancements and then we teach them to robots. We also determine which tasks people should do and which robots should do. When it comes to technology, the human touch is always required.